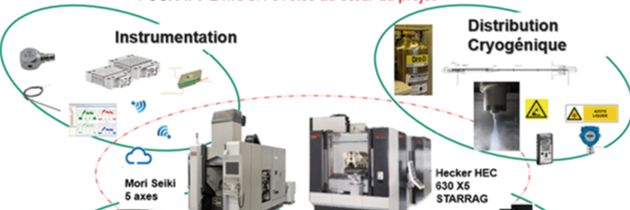
L’Industrie du Futur : le point de vue d’un mécanicien
L’Industrie du Futur apporte au mécanicien des méthodes et outils qui atteignent leur maturité et répondent aux promesses. La chaîne numérique de développement rapide de produit permet de concevoir, industrialiser, produire, maintenir et traiter la fin de vie des produits. À Saint-Dié-des-Vosges, le pôle VirtuReal travaille sur cette chaîne numérique depuis 1991, avec un focus sur le développement d’un procédé de Fabrication Additive propriétaire, la Stratoconception, et des travaux de R&D en usinage dont l’assistance cryogénique. Concernant les logiciels, des suites capables de gérer le jumeau numérique intègrent les outils comme la CFAO (Conception et Fabrication Assistée par Ordinateur), la simulation numérique (avec l’optimisation), le PLM (Product Life Management). Par ailleurs les travaux de R&D sur les technologies d’obtention de pièces et produits s’intensifient ouvrant des nouveaux possibles.
Impression 3D ou Fabrication Additive ?
L’Impression 3D est le terme utilisé dans le grand public, la « Fabrication Additive » est utilisée dans l’Industrie, notamment dans l’Industrie de la Mécanique. Plutôt que « Fabrication Additive », il faudrait dire les procédés de fabrication additive. En effet la norme ISO 17296-2 de 2015 définit sept familles de procédés :
- Polymérisation d’une résine sous l’action d’un laser,
- Projection de gouttes de matériau,
- Projection d’un liant sur un substrat de type poudre,
- Solidification de poudre sous l’action d’une source d’énergie de moyenne à forte puissance (laser ou faisceau d’électrons),
- Projection de poudre (ou fusion de fil) dans un flux d’énergie (laser ou plasma,)
- Fusion de fil au travers d’une buse chauffante,
- Assemblage de couches à partir de feuilles ou de plaques découpées.
Grâce à l’ensemble de ces procédés, nous pouvons obtenir des pièces de petites (quelques microns) ou de grandes tailles (plusieurs mètres), dans toutes les familles de matériaux (métaux, polymères, bois, céramiques, bétons, verres …). Chaque procédé a bien sûr des avantages et des inconvénients.
Outillage rapide en acier réalisé en Stratoconception avec des canaux de régulation thermique conforme pour l’injection de culasse de moteur automobile (Source : CIRTES).
Les développements technologiques au cœur du projet FCCN-IP. (source consortium CIRTES, Mécachrome, Evatec Tools, GIP InSIC).
Ces procédés ont été développés dès les années 1980 pour obtenir des maquettes de formes puis rapidement des prototypes fonctionnels, on parlait alors de prototypage rapide
Ensuite des chercheurs ont eu l’idée de fabriquer des outillages en utilisant ces procédés pour fabriquer des pièces en série sur les procédés classiques (fonderie, injection plastique…). On a alors parlé d’outillage rapide. Industriellement il s’agit d’un des usages de la Fabrication Additive le plus abouti (MRL entre 8 et 10).
La Fabrication Directe, qui signifie une pièce bonne obtenue directement par la « Fabrication Additive », est plus récente. La question de la rentabilité économique par rapport aux autres procédés est très présente. Son application se trouve dans des secteurs de pièces uniques comme le médical avec les prothèses, de petites séries comme l’aéronautique ou le militaire ou en maintenance pour réparer rapidement une machine sur une chaîne d’assemblage automobile par exemple. (Voir images page précédente).
L’usinage cryogénique
Pour usiner des matériaux métalliques, les machines-outils utilisent de l’huile de coupe. Le premier rôle de la lubrification est la gestion de la thermique lors de l’usinage. Le comportement du matériau étant très dépendant de la température, il faut usiner dans une plage de température maîtrisée pour obtenir une pièce de qualité au niveau de la géométrie, de l’état de surface et de la métallurgie de la pièce. L’huile de coupe permet également d’évacuer les copeaux. Le personnel présent dans un atelier est exposé au brouillard de microgouttelettes d’huile. Les risques pour la santé sont l’inhalation de cet aérosol et l’exposition cutanée. Des agents microbiologiques se développent dans les bains d’huile. La pièce usinée et les copeaux sont souillés par le fluide de coupe. Ils doivent être nettoyés pour pouvoir utiliser la pièce et pour recycler les copeaux. La pollution la plus facile à enlever étant celle qui n’a pas été produite, plusieurs chercheurs ont proposé de remplacer l’huile par un fluide cryogénique. Les deux familles de fluide sont le CO2 supercritique et l’azote liquide.
Le PIA, Bpifrance et La Région Grand Est financent le projet PSPC FCCN-IP (French Cryo Cut Network. Innovation & Production Partagées), dont les partenaires sont CIRTES (chef de file), Mécachrome, Evatec Tools et l’Institut Supérieur d’Ingénierie de la Conception. L’usinage cryogénique est une réelle rupture pour la filière de la mécanique industrielle par les très hautes performances techniques accessibles, les impacts économiques qui redonnent de la compétitivité, le changement induit chez les différents acteurs, et une amélioration sans précédent des aspects HSE en usinage.
Les travaux du projet portent sur la maîtrise de la distribution cryogénique, l’instrumentation, la surveillance/monitoring du procédé, l’optimisation de la conception des outils de coupe. (Voir illustration ci-dessus)
L’Industrie du Futur repose ainsi sur le développement des outils numériques, principalement logiciels à disposition des industries de la mécanique, mais aussi sur des ruptures technologiques dans le domaine de la mise en forme de matériaux comme la fabrication additive ou l’usinage cryogénique.
Sur ces deux thématiques, l’industrie française peut s’appuyer sur l’excellence de la recherche nationale et des filières industrielles structurées.
À Saint-Dié-des-Vosges, le Pôle VirtuReal est un moteur du développement de ces deux thématiques technologiques majeures pour l’industrie mécanique nationale, notamment avec la structuration récente d’ADDAGE, la Filière de fabrication additive Grand-Est.
Arnaud DELAMÉZIÈRE
est Directeur de l’Institut Supérieur d’Ingénierie de la Conception et Professeur de l’Institut Mines-Télécom. Son parcours scolaire l’a mené de l’ENS Cachan à Mines ParisTech puis à un doctorat à l’Université de Technologie de Compiègne. Spécialiste en simulation numérique et optimisation, la Direction de la Formation d’Ingénieur Mines Nancy spécialité Génie Mécanique de 2004 à 2015 a conforté sa réflexion sur les compétences en conception mécanique et mécanique.