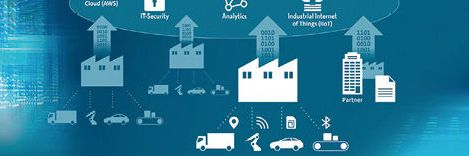
Implementation of the Industry 4.0 concept in an Automotive Group
This year, we have the tenth anniversary of the German strategic initiative for industrial investment of several million euros across Europe. Some of the early results, such as an improved interconnection between the factory and management, made it easier to get through the pandemic. Other solutions currently implemented, such as the most recent Volkswagen “Industrial Cloud” experiment, will finally allow to gain in productivity, efficiency and flexibility, in order to address the challenges of the future in the best way. We are going through one of the most intense times of change in history and all industry or company have to face this new challenge.
Traditional competitive advantages change continuously and impose agility and clarity of objectives. The COVID19 global pandemic crisis has shown that the challenge is not to do detailed long-term planning, but rather to have a successful model structured to manage the transformation process in a responsive, flexible and sustainable manner. Supporting this idea is Industry 4.0, ten years after the first time German Chancellor Merkel spoke about it. Industry 4.0 serves to boost the economy and above all to prepare Europe for the challenges of the future.
The expression was born as the title of one of the 10 strategic development projects of the German state (Strategy 2020). In many ways, efforts by Germany and other countries in this direction have reduced the negative impact of the pandemic. Just think of the possibility of working remotely and the increased use of the artificial intelligence (AI) in factories.
With 4.0 we mean the fourth industrial revolution, after mechanization, industrialization and automation. The new revolution is given...