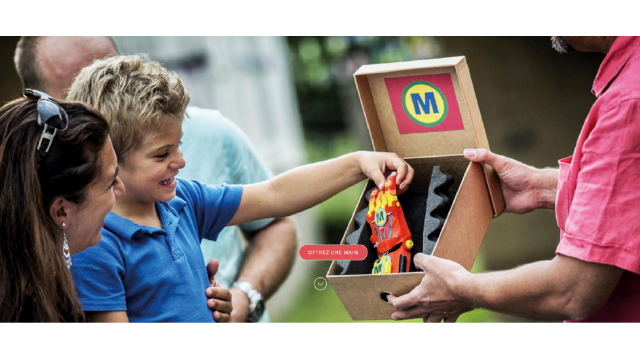
Revue TELECOM 193 - De l'impression 3D à la biotech associative, retour d'expérience
DE L'IMPRESSION 3D A LA BIOTECH ASSOCIATIVE, RETOUR D'EXPERIENCE
Par Fabrice Léonard (2003) dans la revue TELECOM n° 193
Dans les dernières décennies, nous avons vu apparaitre un grand nombre de technologies aux potentiels énormes et à l’ascension exponentielle.
Certaines ont été bien plus loin que ce qu’on pouvait imaginer et ont radicalement changé nos modes de vie. L’impression 3D est sans aucun doute l’une de celle-ci.
On en parle depuis de nombreuses années avec des exemples spectaculaires qui sont bien trop souvent hors de portée de tout à chacun car les usages présentés sont souvent utilisés dans des milieux industriels ou nécessitent un investissement important. Pourtant il est souvent possible de décliner ces technologies dans un contexte moins professionnel mais tout aussi porteur de valeur, c’est le cas de l’impression 3D individuelle.
Petit rappel sur l’impression 3D
L’apport du numérique dans le milieu industriel n’est pas nouveau. La CAO/DAO et même la FAO (Conception, Dessin et Fabrication assistée par ordinateur) existent depuis plusieurs dizaines d’années. La FAO, par exemple, permet de piloter des machines à commandes numériques, qui sont très largement utilisées dans l’usinage ou l’assemblage de pièces.
Alors qu’apporte l’impression 3D de plus ?
A la différence d’un procédé classique de fabrication qui effectue la mise en forme d’un objet par enlèvement de matière (modelage, découpage, usinage, …) l’impression 3D en rajoute. Cela s’appelle la fabrication additive.
Il existe trois grands types d’impression 3D.
• L’impression par dépôt de matière couche par couche. Plus connu sous l'acronyme FFF (Fused Filament Fabrication) ou FFM (Fused Deposition Modeling). Il s’agit de faire passer de la matière (comme par exemple du plastique) dans une tête d’impression chaude qui va la déposer par couche successive.
• L’impression Stereolithography, ou Photopoly-mérisation (SLA - StereoLithographApparatus) qui fonctionne à l’aide d’un laser ultraviolet qui, en frappant une résine sensible aux UV située dans une cuve, va se polymériser au passage du laser. Cela permet notamment de fabriquer des pièces qui serviront de moule.
• L’impression par frittage laser sélectif ou SLS (Selective Laser Sintering). C’est le même principe que l’impression par photopolymérisation, à la différence qu’il n’y a pas de cuve de résine sensible aux UV. Il s’agit cette fois-ci d’utiliser un laser qui va frapper de la poudre de matériaux (ex : polystyrène, verre, nylon, acier, argent, …) qui, au contact du laser va s’assembler créant ainsi la forme que l’on souhaite.
Principe
L’avantage essentiel de l’impression 3D est la rapidité de fabrication. Le principe est le suivant :
On modélise avec un logiciel 3D, on tranche la modélisation avec un « Slicer » (logiciel permettant de découper la modélisation en couche qui sera ensuite envoyée à l’imprimante) et on envoie les commandes d’impression à l’imprimante qui en fonction du type d’imprimante, pourra imprimer la pièce dans différents types de matériaux.
Avec ce principe, on peut aussi bien imprimer une maison en béton, un vélo en bois, une figurine en chocolat, des sushis, du tissus vivant ou une prothèse de main en PLA (polylactic acid ou Polymère biodégradable). C’est de cette expérience dont il va être question dans ce qui suit.
Retour d’expérience de la prise en main, des premières expériences à la fabrication d’objets complexes
J’ai longtemps hésité à acheter une imprimante 3D. Même si je trouvais cette technologie stupéfiante, je ne voyais pas vraiment le besoin de m’en équiper. Je me disais : « c’est trop cher et ça ne m’apportera rien. Et puis, si j’ai vraiment besoin de fabriquer une pièce, je la dessine avec un logiciel 3D comme Fusion360, ThinkerCad ou FreeCAD et j’envoie mon fichier à une société sur Internet qui propose d’imprimer mon fichier 3D moyennant quelque dizaine d’euros ».
Mais avec la chute des prix et l’augmentation de la qualité d’impression, j’ai fini par m’équiper.
Au début, on fabrique les petits modèles fournis avec l’imprimante (ellipse d’ADN, figurines, etc…) et on apprend à bien la régler. (température, niveau, vitesse, etc…).
Ensuite on cherche à améliorer l’imprimante car pour une centaine d’euros, il faut savoir que beaucoup de choses manquent. On va donc rapidement imprimer de nouvelles pièces pour l’imprimante : un support de bobine, un guide filament, des supports de câbles électriques, des roues de réglage pour le plateau d’impression, etc…
De cette manière et très vite la petite imprimante de base et bas de gamme devient une imprimante de bien meilleure facture qui permet de réaliser des pièces de meilleure qualité avec une vitesse d’impression bien plus grande.
Si on est curieux, on trouve différents sites de partage de fichiers d’impression (Cults3D, Thingiverse, MyminiFactory, Free3D, …) et il devient possible d’imprimer tout et n’importe quoi. On rentre alors dans un univers ou l’on a l’impression que tout est faisable : un porte-clefs Suisse, un casse noix, un pot de fleurs Pokemon, un porte carte SD, des clips pour portière de Renault Scenic, des figurines Marvel, un support de manette WII-U, un support d’Iphone, etc…
Par la suite, je décide de dessiner un objet 3D pour l’imprimer. Là, c’est à un autre niveau de complexité, mais je finis par y arriver (avec patience et persévérance). Par exemple, je réalise des rails pour meuble de cuisine Ikéa, un support pour casque à destination de l’Open-Space du bureau ou un support pour un interrupteur électrique Legrand.
Imprimer « utile »
Et puis à force de parcourir forums et groupes de discussion, j’arrive vers l’association « E-nable », qui propose d’imprimer des prothèses mécaniques de main et de bras pour des enfants atteints d’une agénésie ou qui ont subi une amputation. Ce type de prothèses s’enfilent comme un gant et s’enlèvent tout aussi facilement. Elles sont légères, peu couteuse et rapides à produire.
L’association propose, par l’intermédiaire de son site web (https://e-nable.fr), tous les outils pour produire une main et effectue la mise en relation et le suivi des personnes ayant besoin de ce type d’appareillage avec des personnes en mesure de les fabriquer (appelés les « makers »).
Pour devenir « makers » pour l’association E-nable, il faut aimer bricoler, détourner, transformer et proposer un peu de son temps et du matériel pour fabriquer une main pour un enfant qui en a un grand besoin.
Il vous sera tout d’abord demandé de fabriquer une main de test qui sera validée par un coordinateur. Pour cette première étape, Il faut compter une quarantaine d’euros de matériels et environ une trentaine d’heures de travail, y compris le temps d’impression et celui de l’assemblage. Et voilà, vous avez réalisé une main opérationnelle qui va refermer ses doigts grâce à la contraction du poignet.
Ensuite, si votre main est bien faite et opérationnelle, vous serez « validé » comme « maker » et vous pourrez être mis en relation avec une famille. Il faudra alors réaliser un prototype pour s’assurer que celui-ci s’adapte bien au poignet de l’enfant avant de réaliser la main définitive qu’il pourra garder environ 18 à 24 mois.Passé cette période, il faudra alors refaire une nouvelle main avec une nouvelle échelle, car, heureusement, un enfant, ça grandit.
Entre les nouveaux cas d’agénésie (environ 300 enfants par an) et le fait qu’il faut refaire la prothèse tous les 18 mois car les enfants grandissent, l’association à besoin de nombreux « makers ». Alors lancez-vous !
Voila mon retour d’expérience sur l’impression 3D, de l’expérimentation personnelle vers le statut de « maker » à vocation biotech. Je ne peux que vous encourager à participer à ce type de projet. Toutefois, ne le faites que si vous maîtrisez l’impression 3D et que si vous êtes capable de respecter votre engagement.
À PROPOS DE • E-nable France est une association loi de 1901, reconnue d’intérêt général, constituée fin 2015. • Sa mission est de mettre en relation des personnes ayant besoin d’un appareil avec les personnes susceptibles de les fabriquer. • Ses « makers » utilisent l’impression 3D pour fabriquer et offrir des mains à des personnes qui n’ont pas de doigts. |
Biographie de l'auteur
Fabrice Léonard est Manager IT (CTO) au sein de Cegos, Leader européen de la formation professionnelle. Il s’occupe plus particulièrement de projets d'infrastructure pour le système d'information Cegos. Sa mission est de définir les orientations technologiques, concevoir les architectures techniques et encadrer les mises en œuvre. Auparavant, Fabrice a été électronicien en laboratoire, ingénieur réseaux télécoms dans différentes SSII et consultant en système d’information.
Auteur
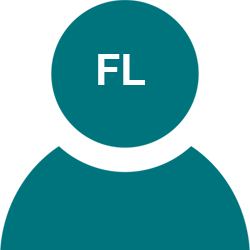